Injection Plastics in Metal Fabrication: Revolutionizing the Industry
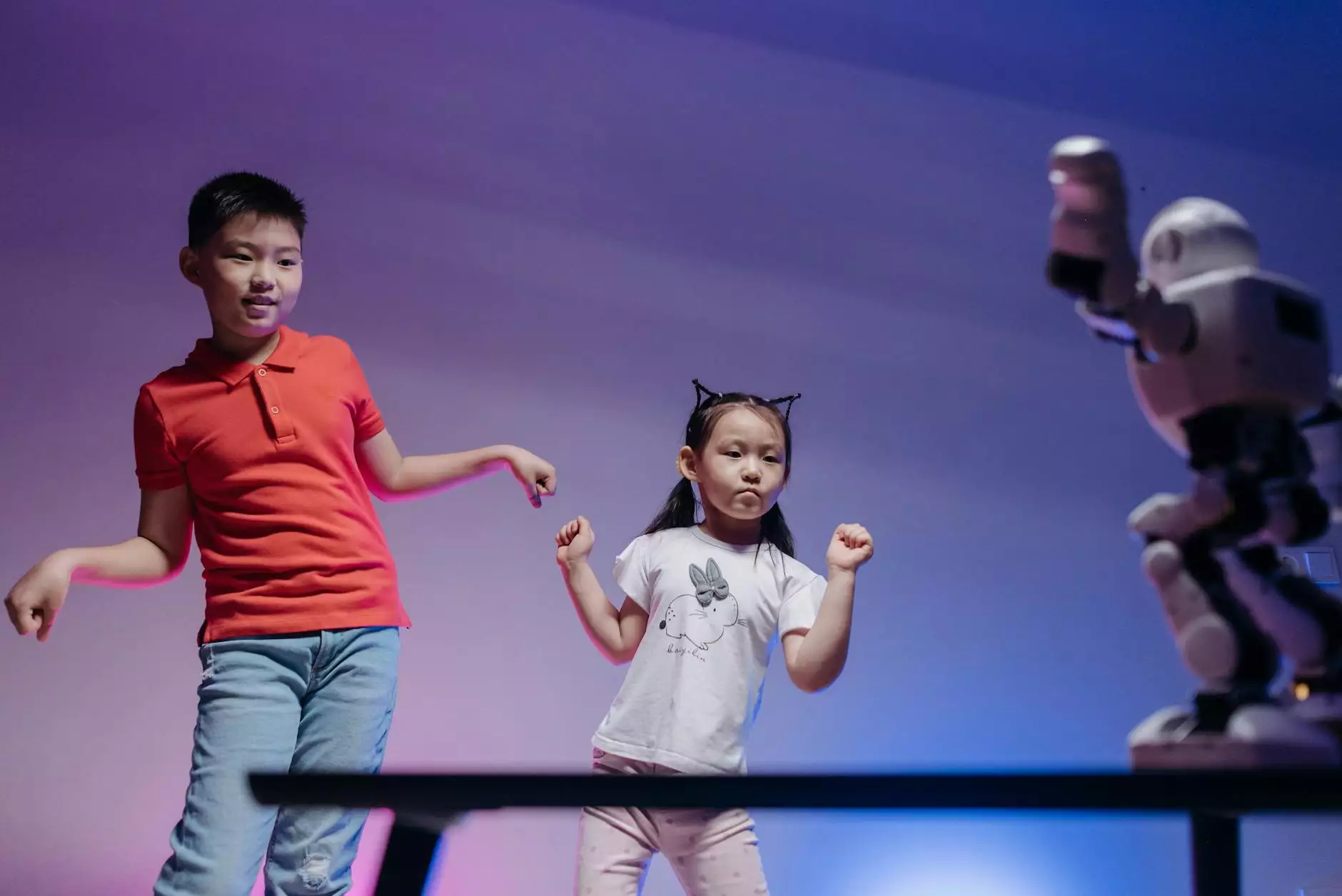
The world of metal fabrication has undergone significant changes in recent years, largely driven by advancements in technology and materials science. One of the most impactful innovations is the integration of injection plastics into traditional fabrication processes. This article aims to explore the role of injection plastics in metal fabrication, highlighting its benefits, applications, and future potential.
Understanding Injection Plastics
Injection plastics refer to the process of creating plastic parts and products through the injection molding technique. During this process, plastic material is melted down and injected into a mold under high pressure. Once cooled, the mold is opened, and the solidified part is ejected. This method offers several advantages:
- High Efficiency: Injection molding allows for rapid production of complex shapes with minimal waste.
- Consistency: It provides uniform quality and precision, making it ideal for mass production.
- Material Diversity: A wide range of thermoplastics and thermosets can be used in the injection molding process.
Metal Fabrication: A Brief Overview
Metal fabrication encompasses various processes utilized to create metal structures and components from raw materials. This field includes techniques such as welding, cutting, bending, and assembling metals into final products. The demand for custom metal fabrications has grown significantly, driven by industries like automotive, aerospace, construction, and many others.
The Intersection of Metal Fabrication and Injection Plastics
As industries evolve, the demand for lightweight, durable, and cost-effective materials has led manufacturers to explore the integration of injection plastics into their metal fabrication processes. Here’s how these two sectors complement each other:
1. Enhancing Product Performance
Combining metals with injection-molded plastics can enhance product performance by providing better strength-to-weight ratios and corrosion resistance. For products that need to withstand harsh environments, the use of specific plastics can protect metal components from abrasion and chemical reactions.
2. Cost Reduction
Using injection plastics in metal fabrication can significantly reduce costs by:
- Minimizing material waste through efficient design and production.
- Shortening manufacturing times since plastic parts can often be produced faster than metal components.
- Lowering shipping costs due to reduced weight of products.
3. Improved Design Flexibility
Plastics offer unique design opportunities that may not be achievable with metals alone. For instance, intricate designs and multi-functional parts can be produced through injection molding, resulting in innovative products that meet modern consumer needs.
Applications of Injection Plastics in Metal Fabrication
The incorporation of injection plastics into metal fabrication processes has yielded remarkable outcomes across various applications:
1. Automotive Industry
In the automotive sector, manufacturers continually seek ways to reduce vehicle weight and improve fuel efficiency. The combination of metal structures with injection-molded plastic parts, such as dashboards, trim, and panels, has proven effective in achieving these goals. Moreover, this fusion can lead to:
- Reduction in assembly time due to the simplified design of multi-component parts.
- Enhanced acoustics and insulation through the use of injected plastic insulators.
2. Aerospace Sector
The aerospace industry demands high-performance materials that can endure extreme conditions. Injection plastics can be used to create components like ducting systems, which must be lightweight yet strong enough to withstand pressure and temperature variations. Benefits include:
- Weight reduction, contributing to fuel efficiency.
- Reduced vibration and noise through the use of plastic insulators.
3. Consumer Electronics
In consumer electronics, the demand for sleek designs and lightweight products has fueled the adoption of injection plastics. Components such as casings, housings, and internal structures are often produced using a combination of metals and plastics, offering:
- Streamlined designs that enhance both functionality and aesthetics.
- Improved durability and impact resistance.
Sustainability in Metal Fabrication with Injection Plastics
Environmental sustainability is becoming increasingly important within the manufacturing sector. The integration of injection plastics into metal fabrication can facilitate greener practices by:
- Using recyclable plastic materials that reduce overall waste.
- Decreasing energy consumption due to shorter manufacturing times.
- Minimizing emissions through improved processes and material management.
Challenges of Integrating Injection Plastics into Metal Fabrication
While the benefits of combining injection plastics with metal fabrication are significant, there are still challenges to consider:
1. Material Compatibility
Finding the right combination of materials that bond effectively can be challenging. Not all metals and plastics can be combined successfully without compromising structural integrity.
2. Manufacturing Process Complexity
The introduction of plastic components can add complexity to manufacturing processes. Careful planning and design are essential to ensure that production is efficient and cost-effective.
The Future of Injection Plastics in Metal Fabrication
The future of injection plastics in the metal fabrication industry holds exciting potential. As demand for lighter, stronger, and more complex products grows, so too will the innovations that marry metals with plastic components.
1. Advancements in Material Science
As research into materials continues, we can expect to see more versatile plastics being developed that can withstand higher temperatures and stresses, making them suitable for even more applications in metal fabrication.
2. Automation and Technology Integration
The rise of automation in manufacturing can streamline the process of integrating injection plastics into metal fabrication, yielding faster production rates, lower costs, and improved product quality.
Conclusion
In summary, the integration of injection plastics into metal fabrication is transforming how industries approach product design and manufacturing. By leveraging the advantages of both metals and plastics, manufacturers can produce innovative, high-quality products that meet evolving consumer demands while also addressing sustainability challenges. As the industry continues to evolve, deepmould.net remains at the forefront of this exciting intersection, dedicated to harnessing the power of injection plastics to drive future growth and innovation.